1X4 Amp Schematics - With Pictures
- WESTGATE
- Donor
- Posts: 495
- Joined: Sep 24 2009, 21:23
- Handle: WESTGATE
- Real Name: randall robles
- Contact:
1X4 Amp Schematics - With Pictures
[Please login or register to view this link]
[Please login or register to view this link]
[Please login or register to view this link]
[Please login or register to view this link]
[Please login or register to view this link]
[Please login or register to view this link]
[Please login or register to view this link]
[Please login or register to view this link]
[Please login or register to view this link]
[Please login or register to view this link]
[Please login or register to view this link]
[Please login or register to view this link]
[Please login or register to view this link]
[Please login or register to view this link]
[Please login or register to view this link]
[Please login or register to view this link]
[Please login or register to view this link]
[Please login or register to view this link]
[Please login or register to view this link]
[Please login or register to view this link]
[Please login or register to view this link]
[Please login or register to view this link]
[Please login or register to view this link]
[Please login or register to view this link]
[Please login or register to view this link]
[Please login or register to view this link]
[Please login or register to view this link]
[Please login or register to view this link]
[Please login or register to view this link]
[Please login or register to view this link]
continued in 1X4 amp schematics "part 2"
[Please login or register to view this link]
[Please login or register to view this link]
[Please login or register to view this link]
[Please login or register to view this link]
[Please login or register to view this link]
[Please login or register to view this link]
[Please login or register to view this link]
[Please login or register to view this link]
[Please login or register to view this link]
[Please login or register to view this link]
[Please login or register to view this link]
[Please login or register to view this link]
[Please login or register to view this link]
[Please login or register to view this link]
[Please login or register to view this link]
[Please login or register to view this link]
[Please login or register to view this link]
[Please login or register to view this link]
[Please login or register to view this link]
[Please login or register to view this link]
[Please login or register to view this link]
[Please login or register to view this link]
[Please login or register to view this link]
[Please login or register to view this link]
[Please login or register to view this link]
[Please login or register to view this link]
[Please login or register to view this link]
[Please login or register to view this link]
[Please login or register to view this link]
continued in 1X4 amp schematics "part 2"
The more watts you swing, the more people you bring. BREAK!
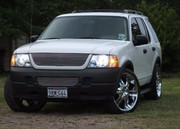
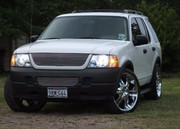
- WESTGATE
- Donor
- Posts: 495
- Joined: Sep 24 2009, 21:23
- Handle: WESTGATE
- Real Name: randall robles
- Contact:
1X4 amp schematics "part 2"
[Please login or register to view this link]
[Please login or register to view this link]
[Please login or register to view this link]
[Please login or register to view this link]
[Please login or register to view this link]
[Please login or register to view this link]
[Please login or register to view this link]
[Please login or register to view this link]
[Please login or register to view this link]
[Please login or register to view this link]
[Please login or register to view this link]
[Please login or register to view this link]
[Please login or register to view this link]
[Please login or register to view this link]
[Please login or register to view this link]
[Please login or register to view this link]
[Please login or register to view this link]
[Please login or register to view this link]
[Please login or register to view this link]
[Please login or register to view this link]
[Please login or register to view this link]
[Please login or register to view this link]
[Please login or register to view this link]
[Please login or register to view this link]
[Please login or register to view this link]
[Please login or register to view this link]
[Please login or register to view this link]
[Please login or register to view this link]
[Please login or register to view this link]
continued on 1X4 "part 3"
[Please login or register to view this link]
[Please login or register to view this link]
[Please login or register to view this link]
[Please login or register to view this link]
[Please login or register to view this link]
[Please login or register to view this link]
[Please login or register to view this link]
[Please login or register to view this link]
[Please login or register to view this link]
[Please login or register to view this link]
[Please login or register to view this link]
[Please login or register to view this link]
[Please login or register to view this link]
[Please login or register to view this link]
[Please login or register to view this link]
[Please login or register to view this link]
[Please login or register to view this link]
[Please login or register to view this link]
[Please login or register to view this link]
[Please login or register to view this link]
[Please login or register to view this link]
[Please login or register to view this link]
[Please login or register to view this link]
[Please login or register to view this link]
[Please login or register to view this link]
[Please login or register to view this link]
[Please login or register to view this link]
[Please login or register to view this link]
continued on 1X4 "part 3"
The more watts you swing, the more people you bring. BREAK!
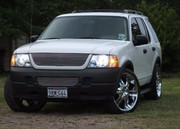
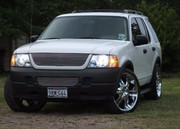
- WESTGATE
- Donor
- Posts: 495
- Joined: Sep 24 2009, 21:23
- Handle: WESTGATE
- Real Name: randall robles
- Contact:
1X4 amp schematics "part 3"
[Please login or register to view this link]
[Please login or register to view this link]
[Please login or register to view this link]
[Please login or register to view this link]
[Please login or register to view this link]
[Please login or register to view this link]
[Please login or register to view this link]
[Please login or register to view this link]
[Please login or register to view this link]
[Please login or register to view this link]
[Please login or register to view this link]
[Please login or register to view this link]
[Please login or register to view this link]
[Please login or register to view this link]
[Please login or register to view this link]
[Please login or register to view this link]
[Please login or register to view this link]
[Please login or register to view this link]
[Please login or register to view this link]
[Please login or register to view this link]
[Please login or register to view this link]
[Please login or register to view this link]
[Please login or register to view this link]
[Please login or register to view this link]
[Please login or register to view this link]
[Please login or register to view this link]
[Please login or register to view this link]
[Please login or register to view this link]
continued in 1X4 amp "part4"
[Please login or register to view this link]
[Please login or register to view this link]
[Please login or register to view this link]
[Please login or register to view this link]
[Please login or register to view this link]
[Please login or register to view this link]
[Please login or register to view this link]
[Please login or register to view this link]
[Please login or register to view this link]
[Please login or register to view this link]
[Please login or register to view this link]
[Please login or register to view this link]
[Please login or register to view this link]
[Please login or register to view this link]
[Please login or register to view this link]
[Please login or register to view this link]
[Please login or register to view this link]
[Please login or register to view this link]
[Please login or register to view this link]
[Please login or register to view this link]
[Please login or register to view this link]
[Please login or register to view this link]
[Please login or register to view this link]
[Please login or register to view this link]
[Please login or register to view this link]
[Please login or register to view this link]
[Please login or register to view this link]
continued in 1X4 amp "part4"
The more watts you swing, the more people you bring. BREAK!
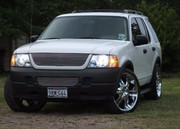
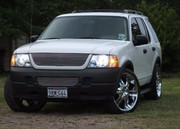
- WESTGATE
- Donor
- Posts: 495
- Joined: Sep 24 2009, 21:23
- Handle: WESTGATE
- Real Name: randall robles
- Contact:
1X4 amp schematics "part 4"
[Please login or register to view this link]
[Please login or register to view this link]
[Please login or register to view this link]
[Please login or register to view this link]
[Please login or register to view this link]
[Please login or register to view this link]
[Please login or register to view this link]
[Please login or register to view this link]
[Please login or register to view this link]
[Please login or register to view this link]
[Please login or register to view this link]
[Please login or register to view this link]
[Please login or register to view this link]
[Please login or register to view this link]
[Please login or register to view this link]
[Please login or register to view this link]
[Please login or register to view this link]
[Please login or register to view this link]
[Please login or register to view this link]
[Please login or register to view this link]
[Please login or register to view this link]
[Please login or register to view this link]
[Please login or register to view this link]
[Please login or register to view this link]
[Please login or register to view this link]
[Please login or register to view this link]
[Please login or register to view this link]
[Please login or register to view this link]
[Please login or register to view this link]
[Please login or register to view this link]
continued 1X4 amp schematics "part 5"
[Please login or register to view this link]
[Please login or register to view this link]
[Please login or register to view this link]
[Please login or register to view this link]
[Please login or register to view this link]
[Please login or register to view this link]
[Please login or register to view this link]
[Please login or register to view this link]
[Please login or register to view this link]
[Please login or register to view this link]
[Please login or register to view this link]
[Please login or register to view this link]
[Please login or register to view this link]
[Please login or register to view this link]
[Please login or register to view this link]
[Please login or register to view this link]
[Please login or register to view this link]
[Please login or register to view this link]
[Please login or register to view this link]
[Please login or register to view this link]
[Please login or register to view this link]
[Please login or register to view this link]
[Please login or register to view this link]
[Please login or register to view this link]
[Please login or register to view this link]
[Please login or register to view this link]
[Please login or register to view this link]
[Please login or register to view this link]
[Please login or register to view this link]
continued 1X4 amp schematics "part 5"
The more watts you swing, the more people you bring. BREAK!
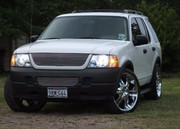
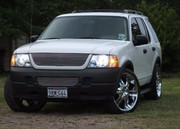
- WESTGATE
- Donor
- Posts: 495
- Joined: Sep 24 2009, 21:23
- Handle: WESTGATE
- Real Name: randall robles
- Contact:
1X4 amp schematics "part 5"
[Please login or register to view this link]
[Please login or register to view this link]
[Please login or register to view this link]
The more watts you swing, the more people you bring. BREAK!
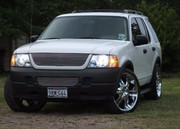
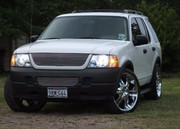
- WESTGATE
- Donor
- Posts: 495
- Joined: Sep 24 2009, 21:23
- Handle: WESTGATE
- Real Name: randall robles
- Contact:
Re: 1X4 amp schematics "part 5" continued
[Please login or register to view this link]
[Please login or register to view this link]
[Please login or register to view this link]
[Please login or register to view this link]
[Please login or register to view this link]
[Please login or register to view this link]
[Please login or register to view this link]
[Please login or register to view this link]
[Please login or register to view this link]
[Please login or register to view this link]
[Please login or register to view this link]
[Please login or register to view this link]
[Please login or register to view this link]
[Please login or register to view this link]
[Please login or register to view this link]
[Please login or register to view this link]
[Please login or register to view this link]
[Please login or register to view this link]
[Please login or register to view this link]
[Please login or register to view this link]
[Please login or register to view this link]
[Please login or register to view this link]
[Please login or register to view this link]
[Please login or register to view this link]
parts list and build instructions
Designator Description QTY Code Check
R1, R4, R5, & R15 4.7Ω 2W Carbon Film Resistor 4 Yellow-Violet-Gold
R2, R10, R11
R12, & R13 100Ω 2W Carbon Film Resistor 5 Brown- Black- Brown
R3, R6, R7
R8, & R9 10Ω 1/2W Carbon Film Resistor 5 Brown-Black-Black
R14 100Ω 5W Metal Film Resistor 1 Brown- Black- Brown
VR1 100Ω 2W Potentiometer 1 Labeled
C1 100~180 pf Silver Dipped Mica Capacitor 1 100~180 / 500V
C2, C3, C4, C9, &
C23 1000 pf Silver Dipped Mica Capacitor 5 1000 or 102 / 500V
C5, C6, C7, C8 .1 uf Ceramic Disc Capacitor 4 104 or .1
C10, C11, C12
C13, & C14 120 pf Silver Dipped Mica Capacitor 5 120 or 121 / 500V
C19, C20, C21, C22
C25, C26, C27, C28 .01 uf Ceramic Disc Capacitor 8 103 or .01
C15, & C16 330pf Silver Dipped Mica Capacitor 2 330 or 331 /500V
C17, & C18 820pf Metal Clad Capacitor 2 820
C24 150 pf Metal Clad Capacitor 1 150
C29 22 uf Electrolytic Capacitor 1 22 uf / 25V
C30 10 pf Ceramic Disc Capacitor 1 10
VC1 Mica Compression Trim Capacitor 1 465
D1 3A / 1000V PIV Silicon Rectifier 1 1N5408
D2 1A / 1000V PIV Silicon Rectifier 1 1N4007
D3 Glass Signal Diode 1 1N4148
D4 LED Indicator assy. 1 Blue LED / Resistor Pkg.
TR1 Driver Section Power Transistor 1 SD1446 / 2SC2879 (See Note)
*Above transistor depends on which model is being constructed – SD1446=650V+ / 2SC2879=650V+ HDV
TR2, TR3
TR4, & TR5 200 Watt RF Power Transistor 4 2SC2879
TR6 NPN Switching Transistor / TO-92 1 PN2222A
CHK5, 8, 9, 10
11, 12, & 13 ½” x ½” Ferrite Core 7
CHK2, 3, 4, 6, & 7 ¼” x ½” Ferrite Core 5
Designator Description QTY Code Check
T1, T3, & T4 ½” x ½” Ferrite Transformer Core 3
T2 ½” x 1” Ferrite Transformer Core 1
T5, T6 ½” x 2” Ferrite Transformer Core 2
SW1 SPST Switch 1
RLY1 DPDT Relay 12V Coil /10A Contacts 1
FAN1 4.7” Fan Assy. 1
FG1 4.7” Fan Guard 1
Conn1, Conn2 Panel Mount SO239 UHF Connector 2
Conn3 ¼” Stereo Phone Jack 1
Cabinet Aluminum Enclosure Assy. 1
HS1 Aluminum Heat Sink 1
CB1 Pre-Drilled Copper Clad Circuit Board 1
CB2 Copper Clad Circuit Board 5-1/8” x 3/4” 1
PS1, & 2 2 Position Pre-Cut Transistor / Pill Strips 2
PS3, & 4 4 Position Pre-Cut Transistor / Pill Strips 2
SCK1 LED Mounting Clip (with D4) 1
KB1 Control Knob 1
WIRE-1 28” Length of #20 Silver/Teflon Wire 1
WIRE-2 108” Length of #16 Silver/Teflon Wire 1
WIRE-3 3” Length of #14 Silver/Teflon Wire 1
WIRE-4 25” Length of #20 Hook-up Wire (Color 1) 1
WIRE-5 18” Length of #20 Hook-up Wire (Color 2) 1
WIRE-6 12” Length of #10 Red Power Cable 1
WIRE-7 12” Length of #10 Black Power Cable 1
COAX 12” Length RG316 Coax 1
HDW1 Hardware Kit (See Below)
SHCS #4 40 x ¼” Socket screw 14
SHCS #6 32 x ¼” Socket screw 12
Pan Head Sheet Metal Screw 6
Pan Head Machine Screw #6 32 x ½” 8
#6 Lock Washer 6
#6 32 TPI Machine Nut 4
#6 Solder Lug 3
Pan Head Machine Screw #8 32 x ¾” 4
#8 Lock Washer 3
#8 32 TPI Machine Nut 4
Rubber Feet 4
Rubber Grommet 1
Scrap circuit board material 1
Heat sink lubricant 1
Label Sheet 1
4” Cable Tie 4
Tools Needed: Standard electronic hand tools consisting of but not limited to:
Diagonal wire cutters (4-1/2” flush-cut are the best)
Needle nose pliers (4-1/2” with 1/8” dia. tips for shaping component leads, not those super long ones.)
Good pair of tweezers (Serrated jaws are best)
De-soldering tools if needed (Solder Wick, Manual solder sucker, Pace or equiv. powered de-solder station)
Everybody has their favorite hand tools that they use to perform a particular task, so the following pages will only list
tools as a heads-up of some special items that are needed. The use of common sense is your best tool.
Assembly Instructions
Step 1
Parts Needed: Heat Sink (HS1)
Circuit Board (CB1)
1ea. 200 Watt RF Power Transistors (TR2)
4ea. SHCS #4-40 Socket Machine Screw
Tools Needed: Ultra Fine Sharpie Marker
Power Drill (Battery powered is best)
1/8” drill bit
3/32” dill bit (#40 size works better)
Center Punch
4-40 Tap & Handle (Needed if 3/32” drill bit used)
Procedure:
1, Enlarge the six holes in the main circuit board as shown in photo frame #1. Position circuit board on top of heat
sink as shown in photo frame #2 with the front edge of the board flush with the front edge of the heat sink.
Center the circuit board on heat sink as to have about 3/8” over-hang on each side. Mark heat sink though the four
holes of board as indicated in the photo.
2, Remove board and enlarge the four holes used to mark the heat sink by using the 1/8” drill bit as indicated in photo
frame #2.
3, Use the center punch to mark drill points on heat sink. Bore the four drill points to a depth of about 3/8 of an inch
with the 3/32” / #40 drill bit. If a 3/32” drill bit is used, then the four holes should be threaded with the 4-40 tap. If a
#40 bit is used, the #4-40 x ¼” screws will self tap.
4, Return board to heat sink and mount with the four #4-40 socket machine screws. Carefully place the power the
transistor in the #2 front cut-out and mark the heat sink at the two transistor mount drill points. Carefully remove the
transistor and do the same with the four rear remaining cut-outs. (The #1 front cut-out is not used for this amp
configuration) Return the transistor to its container. Remove circuit board from heat sink and bore the 10 holes
using the same techniques used in procedure 3 with one exception, after boring the ten holes, dress the surface of the
heat sink so that the bored holes are clean and flush. It is of the utmost importance that when the transistors are
mounted, they make complete and full contact with the heat sink. A good counter sink bit turned by hand can assist in
this task. When finished, slide a straight edge across heat sink to check for inconsistencies.
5, Remount the circuit board on heat sink. At this point, the assembly should look as that in photo frame #3
Step 2
Parts Needed: Circuit board / heat sink assy.
6 ea. Pan Head sheet metal screws
1 ea. DPDT Relay (RLY1)
1 ea.5-1/8” x 3/4” copper clad circuit board (CB2)
Pre-cut transistor / pill strips (PS1, 2, 3, & 4)
Bottom half of aluminum enclosure (Cabinet)
2ea. Panel Mount SO239 UHF connector (Conn1 & Conn2)
4ea. Pan Head machine screw #6-32 x ½”
2ea. #6 lock washer
4ea. 32 TPI machine nut
2ea. #6 solder lug
Tools Needed: Ultra Fine Sharpie Marker
5 Minute Epoxy
#2 Phillips screw driver
Pliers or wrench for #6 machine nuts
Procedure:
1, Mount both SO239 UHF connectors from the inside of the enclosure making sure that the cut-out on the center
conductor of the connector is facing up. Use the lock washers on the upper mounting holes and the solder lugs on the
lower. Tip: Set the nuts on the lower screws so that one of the flats of the nut is facing down as to allow the bending
of the solder lug. This will provide clearance that may be needed later. See photo frame #4 for reference.
2, Bend solder lugs up as shown in photo frame #4. Lower circuit board / heat sink assy. into the enclosure and slide
under the two bent up solder lugs all the way back until it is against the back of the enclosure. At this point the six
mounting holes on the right and left sides of the circuit board should line up with the six pre-drilled holes in the
enclosure. Mount the circuit board to enclosure using at least four of the six pan head sheet metal screws.
See photo frame #5 for reference.
3, Position DPDT relay with the terminals forward, and in such a way that the two terminals of the relay coil are on
the bottom and the relay itself is centered between the two UHF connectors and against the rear panel of the
enclosure. Mark the two front corners of the relay on the main circuit board as shown in photo frame #6. Now
position the 5-1/8” x 3/4” copper clad circuit board (foil side up) just in front of the rear main circuit board mounting
screws; and centered on the main circuit board. Mark the two front corners of the 5-1/8” x 3/4” copper clad circuit
board on the main circuit board as shown in photo frame #6. Remove the 5-1/8” x 3/4” board and relay, and set aside.
Remove the mounting screws, and the main circuit board / heat sink assy. from the enclosure.
4, Reposition on the main circuit board / heat sink assy. the 5-1/8” x 3/4” circuit board and relay. (Remember, the two
coil terminals of the relay are at the bottom) Now position the four transistor / pill strips (foil side up) as shown in
photo frame #7.
It is important to read the following in its entirety, as the next process must be performed in one fluid action.
Once you get a good feel where everything needs to be located, mix some 5 minute epoxy where the final amount of
the two mixed components is about the diameter of a quarter dollar and 3/16” high. The previous statement for the
quantity is just for reference, but should be enough to perform the next process. Once the epoxy is good and mixed,
remove the previously positioned components one a time starting with the first pill strip. Apply a light coating of
epoxy to the bottom, reposition right back where it came from. Do the same with the rest of the pill strips. Now
mount the 5-1/8” x 3/4” circuit board at its assigned location. Take the rest of the mixed epoxy and apply to the relay
and place at its marked position. Now go back and reposition any of the components that may have shifted.
As the epoxy sets, remove any extra that may have oozed over the edge at the rear of the relay.
Take a break and have a cup of coffee. Page5
Step 3
Parts Needed: Circuit board / heat sink assy.
RF Power Transistors (TR1, TR2, TR3, TR4, & TR5)
Ferrite Transformer Cores (T1, T2, T3, T4, T5, & T6)
10ea. #4-40 x ¼” Socket machine screws
Tools Needed: 3/32” T-handle Allen wrench (Regular Allen wrench may be used)
Soldering Iron (A good 40~50 watt iron with a 1/16” chisel tip is best)
60/40 resin core solder or equiv. (We use Kester 63/37 @ .031”)
Scrap circuit board material (Included in hardware kit)
Heat sink lubricant (Included in hardware kit)
X-acto knife or Olfa knife
Small 1/8” blade straight slot screw driver (Jewelers type is best)
Procedure:
1, Make sure that all five transistor mounting wells are clear of epoxy ooze (Trim with X-acto knife if needed) and
clean heat sink in the transistor wells with a Q-tip to remove any debris. Trim the corner of the plastic bag containing
the heat sink lubricant. Squeeze equal amounts of lubricant into the center of each transistor wells until all of the
lubricant is used. Align the transistor marked SD1446 / 2SC2879 (TR1) over the front well shown in photo frame #8.
Notice that the collector leg of the transistor has a bevel cut in it, and should be pointing to the right. Firmly push
straight down on top of the transistor until it is fully and completely seated. Be very careful not to bend the mounting
tabs of the transistor as they are made of soft metal. Seat the other four transistors marked 2SC2879 (TR2, TR3, TR4,
& TR5) in the rear four wells with their collector legs pointing to the rear. When finished, the assy. should look just
like photo frame #8.
2, This is another point at which we need to be very careful, as we don’t want to twist off the head of any of the #4-40
socket machine screws. With all the transistors fully seated, thread the machine screws through the mounting tabs of
each of the transistors and into the heat sink. Just make them good and snug, not super tight. Believe me; you don’t
want to have to deal with drilling out a steel #4 screw mounted in aluminum. This is supposed to be fun!
If you used a #40 drill bit when boring the transistor mounting holes, the #4-40 screws will self thread. However if
there is undo resistance, back off a couple turns and them continue the self threading process. Once all the transistors
are mounted, bend the legs as instructed in photo frame #9.
3, Gentlemen, heat up your soldering irons! We will presume you have good soldering skills, so we will not get into a
soldering lesson. However, if there are any questions, please give us a call or Email. Solder the emitter legs of each
transistor to the main circuit board assy. as shown in photo frame #10. Take the 1/2” long ferrite transformer core
(T1) and look at each end, you will notice that on one of the ends, the two brass tubes that comprise the primary
winding is not connected. The non connected side from now on will be referred to as the “front” of this and all
transformers. On the front of the transformer you will also notice that the two solder pads may narrow on one side,
this will be considered the bottom edge and also the side that will be soldered to the pill strips. See photo frame #11.
(On transformers that do not narrow, either edge can be soldered to the pill strips.)
4, Take one of the 1/2” long ferrite transformer cores which will become (T1) and set the front end of the transformer
with the bottom edge down on the pill strip at the base leg of (TR1). Place the scrap piece of circuit board material
under the rear of the transformer to keep it level. Adjust the transformer so that the separation cut in the pill strip is in
the center between the two solder pads of the transformer and the bottom front edge just touches the base leg of the
transistor (TR1). Carefully solder each of the transformer solder pads to the pill strip pads on which they sit by
starting on one side and then moving to the next, while doing so let the base leg of power transistor become soldered
to the pill strip pads as well. Use enough solder as to create a good filet that will help support the transformer. See
photo frame #12. Remove the scrap circuit board material and set aside.
5, Rotate the assy. 180º on the work surface. Take the 1” long ferrite transformer core (T2) and set the front end of
the transformer with the bottom edge down on the pill strip at the collector leg of (TR1). Place the scrap piece of
circuit board material under the rear of the transformer to keep it level. Adjust the transformer so that the separation
cut in the pill strip is in the center between the two solder pads of the transformer and the bottom front edge just
touches the collector leg of the transistor (TR1). Carefully solder each of the transformer solder pads to the pill strip
pads on which they sit by starting on one side and then moving to the next, while doing so, let the collector leg of the
power transistor become soldered to the pill strip pad as well. Use enough solder as to create a good filet that will
help support the transformer. See photo frame #13. Remove the scrap circuit board and set aside.
6, Rotate the assy. to the left 90º on the work surface. Take one of the remaining two 1/2” long ferrite transformer
cores which will become (T4) and set the front end of the transformer with the bottom edge down on the part of the
pill strip that coincides with the base legs of transistors (TR4, & TR5). Place the scrap piece of circuit board material
under the rear of the transformer to keep it level. Adjust the transformer so that the separation cut in the pill strip is in
the center between the two solder pads of the transformer and the bottom front edge just touches the base legs of
transistors (TR4, & TR5). Carefully solder each of the transformer solder pads to the pill strip pads on which they sit
by starting on one side and then moving to the next, while doing so let the base legs of the power transistors become
soldered to the pill strip pad as well. Use enough solder as to create a good filet that will help support the
transformer. See photo frame #14. Remove the scrap circuit board material and set aside.
7, Take the remaining 1/2” long ferrite transformer core which will become (T3) and set the front end of the
transformer with the bottom edge down on the part of the pill strip that coincides with the base legs of transistors
(TR2, & TR3). Place the scrap piece of circuit board material under the rear of the transformer to keep it level.
Adjust the transformer so that the separation cut in the pill strip is in the center between the two solder pads of the
transformer and the bottom front edge just touches the base legs of transistors (TR2, & TR3). Carefully solder each
of the transformer solder pads to the pill strip pads on which they sit by starting on one side and then moving to the
next, while doing so let the base legs of the power transistors become soldered to the pill strip pad as well. Use
enough solder as to create a good filet that will help support the transformer. See photo frame #14. Remove the
scrap circuit board material and set aside.
I know we keep repeating ourselves, but it’s just so we don’t make any mistakes.
8, Rotate the assy. 180º on the work surface. Take one of the two 2” long ferrite transformer cores which will become
(T5) and set the front end of the transformer with the bottom edge down on the part of the pill strip that coincides with
the collector legs of transistors (TR2, & TR3). Place the scrap piece of circuit board material under the rear of the
transformer to keep it level. Adjust the transformer so that the separation cut in the pill strip is in the center between
the two solder pads of the transformer and the bottom front edge just touches the collector legs of transistors (TR2, &
TR3). Carefully solder each of the transformer solder pads to the pill strip pads on which they sit by starting on one
side and then moving to the next, while doing so let the collector legs of the power transistors become soldered to the
pill strip pad as well. Use enough solder as to create a good filet that will help support the transformer. See photo
frame #15. Remove the scrap circuit board material and set aside.
9, Take the remaining 2" long ferrite transformer core which will become (T6) and set the front end of the
transformer with the bottom edge down on the part of the pill strip that coincides with the collector legs of transistors
(TR4, & TR5). Place the scrap piece of circuit board material under the rear of the transformer to keep it level.
Adjust the transformer so that the separation cut in the pill strip is in the center between the two solder pads of the
transformer and the bottom front edge just touches the collector legs of transistors (TR4, & TR5). Carefully solder
each of the transformer solder pads to the pill strip pads on which they sit by starting on one side and then moving to
the next, while doing so let the collector legs of the power transistors become soldered to the pill strip pad as well.
Use enough solder as to create a good filet that will help support the transformer. See photo frame #15.
Remove the scrap circuit board material and discard as it is no longer needed.
Step 4
Parts Needed: Circuit board / heat sink assy.
5 ea. 10Ω 1/2W carbon film resistor (R3, R6, R7, R8, & R9)
5 ea. 120pf @ 500V Silver Dipped Mica Capacitor (C10, C11, C12, C13, & C14)
3 ea. 1000pf @ 500V Silver Dipped Mica Capacitor (C2, C3, & C4)
4 ea. 0.1uf Ceramic Disc Capacitor (C5, C6, C7, & C8)
1 ea. 11” Length of #16 Silver/Teflon wire (WIRE-2)
1 ea. 1A / 1000V PIV Silicon Rectifier (D2) (Small)
Tools Needed: Soldering Iron (A good 40~50 watt iron with a 1/16” chisel tip is best)
60/40 resin core solder or equiv. (We use Kester 63/37 @ .031”)
Procedure:
1, Take the five 10Ω 1/2W resistors, bend and trim as shown in photo frame #16.
Solder these resistors in place as shown in photo frame #17.
2, Take the five 120pf capacitors, bend and trim as shown in photo frame #18.
Solder these capacitors in place as shown in photo frame #19.
3, Take the three 1000pf capacitors, bend and trim as shown in photo frame #20.
Solder these capacitors as shown in photo frame #21.
4, Take the four 0.1uf capacitors, bend and trim as shown in photo frame #22.
Solder these capacitors as shown in photo frame #23.
5, Take the 11” length of #16 wire and make 3 loops through one of the 1/2” x 1/2" ferrite cores (CHK5), strip ends
and bend as shown in photo frame #24. Solder bent end to the middle of the back side of T2, and the straight end to
the 5-1/8” x 3/4” circuit board as shown in photo frame #25.
6, Take the 1A rectifier and attach to the two lower relay coil terminals as shown in photo frame #26, pay attention to
polarity and DO NOT solder yet.
7, Carefully bend-up the two top relay terminals as shown in photo frame #27.
Step 5
Parts Needed: Circuit board / heat sink assy.
1 ea. 13” length of #20 Silver/Teflon wire (WIRE-1)
1 ea. 100pf / 500V Silver Dipped Mica Capacitor (C1)
1 ea. 8” length of #16 Silver/Teflon wire (WIRE-2)
1 ea. 25-1/2” length of #16 Silver/Teflon wire (WIRE-2)
1 ea. 1000pf / 500V Silver Dipped Mica Capacitor (C23)
1 ea. 150pf Metal Clad Capacitor (C24)
1 ea. 45” length of #16 Silver/Teflon wire (WIRE-2)
2 ea. 1/2" x 1/2" Ferrite Core (CHK12, & CHK13)
1 ea. 100Ω 5 Watt Metal Film Resistor (R14)
1 ea. 1” Length of #16 Silver/Teflon wire (WIRE-2)
Tools Needed: Soldering Iron (A good 40~50 watt iron with a 1/16” chisel tip is best)
60/40 resin core solder or equiv. (We use Kester 63/37 @ .031”)
Procedure:
1, Take the 13” length of Silver/Teflon wire and trim 1/4"of insulation from one end only. Insert the non-stripped end
of the wire into the right tube of transformer (T1), bend down the stripped end and solder to the main board as viewed
in photo frame #28. Thread the wire through the left tube from the rear and back through the right tube from the
front. Keep doing this until five (5) winding turns are made, always try to keep the current turn on top of the
previous, however if the windings bundle-up it’s OK, see photo frame #29. Prepare the 100pf capacitor as shown in
photo frame #30. Solder the capacitor to the main circuit board as shown in photo frame #31. Wrap the free
capacitor lead around the stripped wire that exits transformer (T1). Solder and trim capacitor lead, but Do Not trim
the transformer wire as shown in photo frame #32.
2, Rotate circuit board / heat sink assy. 180º. Take the 8” length of #16 Silver/Teflon wire and trim 1/4"of insulation
from one end only. Insert the non-stripped end of the wire into the left tube of transformer (T2), bend down the
stripped end and solder to the main board as viewed in photo frame #33. Wind the transformer in the same manner as
you did with transformer (T1) with the second winding on top of the first, but this time we only need two (2) winding
turns as shown in photo frame #34.
3, Rotate circuit board / heat sink assy. to the left 90º. Take the 25-1/2” length of #16 Silver/Teflon wire, straighten
and fold exactly in half. Mark the center, and trim away 1/4" of insulation from both sides of the center line, for a
total of 1/2" insulation removed. Bend the wire to form the shape shown in photo frame #35. Take one of the
1/2" x 1/2" ferrite cores (CHK12), which will become the power splitter (SLT1) and place over one of the legs of the
wire, slide the core up the wire to within 3/8” of the little loop you just created. Bring the other leg of the wire around
and insert it in the other side of the core, pull tight and re-adjust until this assy. is like that shown in photo frame #36.
Take one of the wires and bring the end around and insert it in the opposite side of the core, pull through to make a
tight winding on the core, do this one more time for a total of two tight windings. Take the other wire and do the
same as the first, although in the opposite direction. To assist in this task, see photo frames #37, #38, & #39.
4, Take one of the wires of the power splitter you just made and run it through the inner most tube of (T3), now take
the other wire of the splitter and run it through the inner most tube of (T4) as shown in photo frame #40.
Position the splitter itself centered right up between the two transformers. Take the wire that is exiting the rear of
(T3) and pull it forward through the left tube as shown in photo frame #41. Now feed the wire back through the right
tube under the first winding as shown in photo frame #42. (As each of these turns is made, keep them as tight as
possible) Feed the wire back through the left tube again under the previous winding as shown in photo frame #43.
Do this one more time; so that there is a total of three windings on (T3), making sure that each new winding is under
the previous. When done, your windings should look like those in photo frame #44. Now do the same to (T4) with
the other wire. Remember to keep each new winding under the previous, and to have three turns of wire just like
(T3). When you are finished, your work should look like photo frame #45. Trim both wires so that there is 3/4 of an
inch protruding from each of the transformers. Remove 1/4" of insulation from the end of each wire, and solder to the
main circuit board as shown in photo frame #46.
5, Now we are going to build the same type of assy. as the power splitter, albeit with a slight modification. But first,
we need to prepare the relay. Take the 1000pf / 500V silver dipped mica capacitor (C23), bend and trim as shown in
photo frame #47. Take this capacitor (C23) and the 150pf metal clad capacitor (C24) and assemble as shown in photo
frame #48. Solder and trim as shown in photo frame #49. Solder this capacitor assy. to the main circuit board as
shown in photo frame #50.
6, OK, here we go. Take the 45” length of #16 Silver/Teflon wire, straighten and fold exactly in half. Mark the
center, and trim away 1/4" of insulation from both sides of the center line, for a total of 1/2" insulation removed.
Bend the wire to form the shape shown in photo frame #51. Take one of the 1/2" x 1/2" ferrite cores (CHK13), which
will become the power combiner (CMB1) and place over one of the legs of the wire, slide the core up the wire to
within 3/8” of the little loop you just created. Bring the other leg of the wire around and insert it in the other side of
the core, pull tight and re-adjust until this assy. is like that shown in photo frame #52. Take one of the wires and
bring the end around and insert it in the opposite side of the core, pull through to make a tight winding on the core, do
this one more time for a total of two tight windings. Take the other wire and do the same as the first, although in the
opposite direction. To assist in this task, see photo frames #53, #54, & #55.
7, Remove the insulation from the combiner (CMB1) in the two locations as shown in photo frame #56.
Take the 100Ω 5W resistor (R14) and wrap the leads around each of the two wires of (CMB1) where the insulation
was removed, as shown in photo frame #57. Solder and trim as shown in photo frame #58. Take the combiner assy.
and insert one of the wires into the inner most tube of transformer (T5), and take the other wire and insert it into the
inner most tube of transformer (T6). Pull these two wires through the transformers until the loop of the combiner
(CMB1) can rest on the relay terminal as shown in photo frame #59. Take the unattached lead of (C23) and insert it
into and through the loop of the combiner (CMB1) and the hole of the relay terminal, bend the capacitor lead straight
up and trim as shown in photo frame #60. Squeeze this connection with non-serrated pliers and solder as shown in
photo frame #61.
8, With the circuit board / heat sink assy. oriented so that the relay is positioned away from you, feed the wire that
protrudes from the right tube of (T5) and insert it into the left tube and pull tight as shown in photo frame #62.
Now take the wire and feed it back through the right tube, pulling toward you while keeping it under the first winding.
After pulling the wire tight, it should look like that in photo frame #63. Keep threading in and out of the transformer
until there are three windings on (T5), remember that each new winding should be under the previous. Refer to photo
frames #64, #65, & #66. Once the windings are nice and tight, trim the end of the wire so that only 1” remains as
shown in photo frame #67. Trim 1/4" of insulation from the end of the wire, and bend around the transformer as
shown in photo frame #68. Solder wire to the main circuit board as shown in photo frame #69. Now perform the
same procedure on (T6), but of course winding in the opposite direction. When you are finished, it should look like
photo frame #70.
9, Take the 1” length of #16 Silver/Teflon wire and remove 3/4" of insulation. The 1/4" of insulation remaining will
hold the strands of wire together. Place this wire across the two top bent terminals of the relay as shown in photo
frame #71. Solder and trim as shown in photo frame #72.
Step 6
Parts Needed: Circuit board / heat sink assy.
1 ea. #465 Mica Compression Trimmer Capacitor (VC1)
2 ea. 4.7Ω Carbon Film Resistor
3 ea. 4-3/4” length of #20 Silver/Teflon wire (WIRE-1)
3 ea. 1/4" x 1/2" Ferrite Core (CHK4, CHK6, & CHK7)
4 ea. 100Ω 2W Carbon Film Resistor (R10, R11, R12, & R13)
4 ea. 0.01uf Ceramic Disc Capacitor (C19, C20, C21, & C22)
1 ea. 1000pf / 500V Silver Dipped Mica Capacitor (C9)
2 ea. 820pf Metal Clad Capacitors (C17 & C18)
2 ea. 330pf / 500V Silver Dipped Mica Capacitor (C15, & C16)
Tools Needed: Soldering Iron (A good 40~50 watt iron with a 1/16” chisel tip is best)
60/40 resin core solder or equiv. (We use Kester 63/37 @ .031”)
Procedure:
1, Take the trimmer capacitor (VC1) and prepare as shown in photo frame #73. Solder to the main circuit board in
such a way that the upper terminal of the trimmer capacitor is under the loop of the power splitter (SLT1) as shown in
photo frame #74.
2, Prepare the two 4.7Ω resistors as shown in photo frame #75. Feed one lead of the resistor assy. down and through
the loop in (SLT1) and the hole in the upper solder tab of (VC1), wrap around and trim as shown in photo frame #76,
(Notice the orientation of the resistors to chose the correct lead to attach). Solder as shown in photo frame #77.
Strip enough insulation from the wire exiting transformer (T2) so that you can wrap the remaining lead of the resistor
assy. as shown in photo frame #78. Solder and trim as shown in photo frame #79.
3, Take the three 4-3/4” lengths of Silver/Teflon wire and prepare the three ferrite cores (CHK4, CHK6, & CHK7) as
shown in photo frame #80. Take the prepared ferrite core CHK4, and solder the longer lead to transformer (T1), and
the shorter 3/4" long lead to the main circuit board as shown in photo frame #81. Take the prepared ferrite core
CHK6, and solder the longer lead to transformer (T3), and the shorter 3/4" long lead to the main circuit board as
shown in photo frame #82. Take the prepared ferrite core CHK7, and solder the longer lead to transformer (T4), and
the shorter 3/4" long lead to the main circuit board as shown in photo frame #83.
4, Prepare four (4) harmonic suppression feed-back circuits by using the 100Ω resistors, the 0.01uf capacitors and the
instructions in photo frame #84. The next process can be a little tricky to hold with your fingers, so we recommend
using a good pair of tweezers. Solder the capacitor end of the feed-back circuit to the forward pill strip, and then bend
the leads as necessary to reach over to the other pill strip. It’s a good idea to line things up before doing any
soldering. Please see photo frames #85, 86, & 87 for component placement.
4, Take the 1000pf Silver Dipped Mica Capacitor (C9) and trim both leads down to 1/4". (Retain these two clippings
for later use) Solder to the front of transformer T2 as shown in photo frame #88.
5, Solder the body of each of the two (2) metal clad capacitors (C17, & C18) to the right solder pad, flush with the top
edge of transformers (T5, & T6) as shown in photo frame #89.
6, Take the two scrap wire clippings from procedure #4, and bend as shown in photo frame #90.
7, Take one of the bent scrap wire clippings and “Hook” the terminal hole of (C17), and squeeze with non-serrated
pliers as shown in photo frames #91 & #92. Do the same to (C18) with the other bent wire clipping.
8, Solder both capacitor wire attachments as shown in photo frame #93. Bend each wire and trim as shown in photo
frame #94. Solder each wire to the left solder pad of it’s transformer as shown in photo frame #95. When finished,
they should look like photo frame #96.
9, Take both of the 330pf silver dipped mica capacitors (C15, & C16) and trim their leads down to 1/4". Solder one
each to transformers (T3, & T4) as shown in photo frame #97.
Step 7
Parts Needed: Circuit board / heat sink assy.
Switching Transistor (TR6)
Glass Signal Diode (D3)
22uf Electrolytic Capacitor (C29)
10pf Ceramic Disc Capacitor (C30)
2 ea. 1/2" x 1/2" Ferrite Core (CHK8, & CHK9)
2 ea. 6-1/2” Length of #16 Silver/Teflon wire (WIRE-2)
1 ea. 3” Length of #14 Silver/Teflon wire (WIRE-3)
Tools Needed: Soldering Iron (A good 40~50 watt iron with a 1/16” chisel tip is best)
60/40 resin core solder or equiv. (We use Kester 63/37 @ .031”)
Procedure:
1, Take the switching transistor and bend legs as shown in photo frame #98. Attach the 22uf electrolytic capacitor to
the switching transistor as shown in photo frame #99, observe polarity. Attach the glass signal diode to the
transistor/capacitor assy. as shown in photo frame #100, observe polarity. Attach the 10pf ceramic disc capacitor as
shown in photo frame #101. Solder and trim as shown in photo frame #102, Do Not solder the full length of the
twisted leads as they will need to be bent in the following procedures.
2, Take the two legs of the T/R relay drive circuit where (TR6’s) collector and (C29’s) positive lead are twisted
together, and insert through the hole in the relays coil terminal where (D2’s) anode is connected. Insert until the body
of the transistor touches the relay, wrap these leads around terminal and trim as shown in photo frame #103. Solder
as shown in photo frame #104. Take the free lead of the disc capacitor and thread though the hole in the relay
terminal, bend over, and trim as shown in photo frame #105, but Do Not solder. Trim the remaining twisted leads as
also shown in photo frame #105. Solder these leads to the main circuit board as shown in photo frame #106.
3, Take the two (2) ferrite cores, the two (2) 6-1/2” lengths of silver/Teflon wire, and prepare as shown in photo
frame #107. Solder the 3/4" leads of each prepared choke (CHK8, & CHK9) to the rear of each transformer
(T5, & T6) as shown in photo frame #108. Carefully bend down the power chokes and solder their leads to the
5-1/8” x 3/4” copper clad circuit board (CB2) as shown in photo frame #109.
4, Take the 3” length of #14 silver/Teflon wire, and completely remove the insulation. Place the wire on the 5-1/8” x
3/4” copper clad circuit board (CB2) so that it overlaps the leads of the two power chokes just soldered. Over-solder
this wire at the same two points the chokes were soldered exactly as shown in photo frame #110. (This wire is for
current flow reinforcement).
Step 8
Parts Needed: Circuit board / heat sink assy.
1 ea. 3A / 1000V Rectifier (D1)
4 ea. .01uf Ceramic Disc Capacitor (C25, C26, C27, & C28)
1 ea. Aluminum Enclosure assy. (Bottom half)
6 ea. Pan Head Sheet Metal Screws
2 ea. 2-1/4” Length of #16 Silver/Teflon wire (WIRE-2)
1 ea. 1/4" Phone Jack (Conn3)
1 ea. SPST Switch (SW1)
1 ea. LED Mounting Clip (SCK1)
1 ea. LED Assy. (D4)
1 ea. 100Ω 2W Potentiometer (VR1)
1 ea. Rubber Grommet
1 ea. 12” Length Red #10 Power Cable (WIRE-6)
1 ea. 12” Length Black #10 Power Cable (WIRE-7)
2 ea. 1/2" x 1/2" Ferrite Core (CHK10, & CHK11)
2 ea. 4” Cable Tie
Tools Needed: Soldering Iron (A good 40~50 watt iron with a 1/16” chisel tip is best)
60/40 resin core solder or equiv. (We use Kester 63/37 @ .031”)
Procedure:
1, Take the 3A rectifier, bend and solder as shown in photo frame #111A, & 111B.
2, Take the four (4) .01uf ceramic disc capacitors, bend and trim as shown in photo frame #112. Solder two (2) of
these capacitors at each end of the 5-1/8” x 3/4" circuit board as shown in photo frame #113, #114, & #115.
3, It’s starting to come together! Take the Circuit board / heat sink assy. and mount in the bottom half of the
enclosure using all six (6) sheet metal screws as shown in photo frame #116. Bend down both solder lugs as shown in
photo frame #117. Solder both lugs to the main circuit board as shown in photo frame #118.
4, Take one of the 2-1/4” long #16 Silver/Teflon wires, remove 1/4" of insulation from both ends and solder to the
output UHF connector as shown in photo frame #119. Take the free end of this wire and insert it into the relay
terminal as shown in photo frame #120. Squeeze this connection with non-serrated pliers to flatten, and solder as
shown in photo frame #121. Take the other 2-1/4” long #16 Silver/Teflon wire, remove 1/4" of insulation from both
ends and solder to the input UHF connector as shown in photo frame #122. Take the free end of this wire and insert it
into the relay terminal next to the lead from (C30) as shown in photo frame #123. Squeeze this connection with nonserrated
pliers to flatten, and solder as shown in photo frame #124.
5, Install phone jack as shown in photo frame #125, it’s a good idea to leave finger tight, as we might want to rotate
later. Prepare switch as shown in photo frame #126. Install switch as shown in photo frame #127. Install LED
mounting clip as shown in photo frame #128. Prepare LED assy. as shown in photo frame #129. Install LED assy. as
shown in photo frame #130. Prepare and install potentiometer as shown in photo frame #131, #132, & #133.
5, Solder the black lead of the LED assy. to the main circuit board as shown in photo frame #134. Attach red wire of
the LED assy. as shown in photo frame #135. Install the rubber grommet as shown in photo frame #136. Remove
1/2" of insulation from one end of each of the #10 power cables, insert the black cable through the grommet and
solder to the main circuit board, insert the red cable through the grommet, install the two (2) ferrite cores, and solder
to the 5-1/8” x 3/4" circuit board over the current reinforcement wire as shown in photo frame #137
Step 9
Parts Needed: Amplifier Chassis
1 ea. 11” Length #20 Hook-up Wire (WIRE-4)
1 ea. 1/4" x 1/2" Ferrite Core (CHK2)
1 ea. 13-1/4” Length #20 Hook-up Wire (WIRE-4)
1 ea. 12” Length #20 Hook-up Wire (WIRE-5)
1 ea. 5” Length #20 Hook-up Wire (WIRE-5)
1 ea. 100Ω 2W Carbon Film Resistor (R2)
1 ea. 4.7Ω 2W Carbon Film Resistor (R1)
1 ea. 12” Length of RG-316 Coax Cable (COAX)
Tools Needed: Soldering Iron (A good 40~50 watt iron with a 1/16” chisel tip is best)
60/40 resin core solder or equiv. (We use Kester 63/37 @ .031”)
Procedure:
1, Prepare the 11” length of hook-up wire and the 1/4" x 1/2" ferrite core as shown in photo frame 138. Attach but do
not solder the 5” lead to the bottom terminal of the switch (SW1), solder the 3-1/4” lead to the 5-1/8” x 3/4" circuit
board as shown in photo frame #139. Take the 13-1/4” length of hook-up wire and remove 1/4" of insulation from
each end, connect one end to the bottom terminal of the switch (SW1) along with the previously attached and solder
as shown in photo frame #140. (Read note below before soldering!)
NOTE: When soldering wires to the switch, make sure that it is in the “Off” (Lever down) position. Also
solder wires as quickly as possible, as excess heat on solder terminals can damage the switch. Route this 13-1/4”
length of #20 wire as shown in photo frame #141. Before attaching the end of this wire, please study photo frame
#142. Once the terminals of the phone jack are identified, attach wire as shown in photo frame #143.
2, Attach and solder one end of the 12” wire as shown in photo frame #144. Route and attach this wire to the phone
jack terminal that will connect to the “RING” of the phone plug when it is inserted, as shown in photo frames #145, &
#146. Use the two (2) cable ties as shown. Take the 5” length of hook-up wire and remove 1/4" of insulation from
each end, attach and solder one end of this wire to the relay coil terminal that already has the cathode of (D2)
attached, as also shown in photo frame #146. Attach the other end of this wire to the phone jack terminal that will
connect to the “RING” of the phone plug when it is inserted, as shown in photo frame #147.
3, Attach and solder the 100Ω resistor as in photo frame #148. Attach and solder the 4.7Ω resistor as shown in photo
frame #149.
4, Prepare the 12” length of RG-316 coax as shown in photo frame #150, & #151. Attach and solder the end of the
coax that is 5” from the shield grounding point to the center terminal of VR1 as shown in photo frame #152. Attach
and solder the other end of coax as shown in photo frame #153. Shape, and route the coax cable, then solder the
shield grounding point the main circuit board as shown in photo frame #154.
5, Oh, I’m sorry. I forgot to say take a break for coffee. By all means more COFFEE!
Step 10
Parts Needed: Enclosure cover assy.
1 ea. 4.7” 12V Fan Assy. (FAN1)
1 ea. 4.7” Fan Guard (FG1)
1 ea. 1/4" x 1/2" Ferrite Core (CHK3)
1 ea. 4.7Ω 2W Carbon Film Resistor (R15)
1 ea. #6 Solder Lug
4 ea. #8-32 x 3/4" Pan Head Machine Screw
3 ea. #8 Lock Washer
4 ea. #8-32 Machine Nut
Tools Needed: Soldering Iron (A good 40~50 watt iron with a 1/16” chisel tip is best)
60/40 resin core solder or equiv. (We use Kester 63/37 @ .031”)
Procedure:
1, Prepare the 4.7Ω resistor as shown in photo frame #155. Prepare the cooling fan as shown in photo frame #156.
Mount the resistor as shown in photo frames #157, #158, & #159. Cut and trim the red / B+ wire of the fan, and
solder to the loop in the resistor lead as shown in photo frame #160. Take the of the red wire you just cut off and
remove 1/4" of insulation from one of the ends, solder the stripped end to the other leg of the resistor as shown in
photo frame #161. Wrap the wire around the ferrite core (CHK3) three (3) times and route wire as shown in photo
frame #162. Cut and strip the black / B- wire of the fan, and solder to the solder lug as shown in photo frame #163.
Modify this solder lug as shown in photo frame #164 so that it may be threaded on a #8 pan head machine screw.
2, Mount the fan assy. to the enclosure cover exactly as shown in photo frame #165 using the #8 machine screws,
lock washer, and nuts. Photo frame #166 shows top view of cover after the fan assy. has been installed.
3, Set the assembled cover to the side, it’s time to test and calibrate your new amplifier.
Step 11
Parts Needed: Amplifier Assy. (Cover not attached)
Tools Needed: -12~20VDC power supply capable of supplying a constant current of 100 amps or better.
-10/11 meter transceiver with a “Dead Key” of 2~4 watts, and a peak envelope power no greater than
35 watts for the 650V+ model, and 45 watts for the 650V+ HDV model.
-Bird 43 watt meter with “peak reading upgrade” and 1000W/ 25~60 MHz. element or equivalent.
-Coax jumper with PL259 connectors at each end.
-1000W dummy load or antenna system with a good standing wave ratio (SWR).
The following are very useful but not necessary
-Sweep audio generator with an adaptor that mates with microphone plug on transceiver and has a
switch that keys transmitter. (We use a Wavetek model 188)
-100 MHz. oscilloscope (We use a Hitachi model V-1065)
-600 MHz. RF spectrum analyzer (We use a Hameg model HM5006
-Other RF taps and connectors as needed.
Procedure: Basic Calibration & Test
1, Connect amplifier as shown in photo frame #167.
2, Power up transceiver and select a mid-band frequency.
3, Keep amplifier “Off” and peak reading function of power meter “Off”.
4, Adjust the amplifier gain control to full counter clock-wise.
5, With the transceiver keyed, and while saying the word “Audio” into the microphone, observe power meter for
forward deflection.
6, Turn amplifier “On”.
7, Key-up transceiver with no audio and slowly increase amplifier gain control to full clock-wise.
Observe power meter for forward deflection.
8, With the transceiver keyed, and while saying the word “Audio” into the microphone repeatedly at 1 second
intervals, adjust VC1 for minimum deflection. This is to mean that when you key-up the transceiver, and during
the one second pause where there is no audio, the meter will have a specific reading. But when there is audio, the
meter needle will deviate forward; adjust VC1 so that this deviation is at a minimum. This is the Root Mean
Square (RMS) output reading. Never operate where the needle swings backwards, as this is an indication of
transistor saturation.
9, Turn “On” the peak reading function of the meter. Key-up transceiver with audio and observe peak output.
10, See photo frame #168 for performance data.
Step 12
Parts Needed: Enclosure Bottom / Amplifier Assy.
Enclosure Cover / Fan Assy.
12 ea. #6 32 x 1/4” Socket screw
4 #6 Pan Head Machine Screw #6 32 x ½”
4 #6 Lock Washers
4 Rubber Feet
Self Adhesive Label Sheet
Tools Needed: -7/64” T-handle Allen wrench (Regular Allen wrench may be used)
-Soldering Iron (A good 40~50 watt iron with a 1/16” chisel tip is best)
60/40 resin core solder or equiv. (We use Kester 63/37 @ .031”)
Procedure:
1, Take the enclosure cover/fan assy. and position as shown in photo frame #169. Cut back the fan power wire to the
length necessary to allow the wire to be soldered to the lug of the 1/4” phone jack that carries switched supply power.
Remove 1/4” of insulation and solder to the appropriate lug as shown in photo frame #169.
2, Position cover/fan assy. on lower chassis and install twelve (12) #6 32 x 1/4” socket screws as shown in photo
frame #170.
3, Install the four (4) rubber feet using the #6 machine screws and lock washers as shown in photo frame #171.
4, Take label sheet, cut apart, peel, and place on rear panel as shown in photo frame #172.
Congratulations, you are now the proud owner of a high quality
high performance HF linear amplifier that you built yourself!
[Please login or register to view this link]
[Please login or register to view this link]
[Please login or register to view this link]
[Please login or register to view this link]
[Please login or register to view this link]
[Please login or register to view this link]
[Please login or register to view this link]
[Please login or register to view this link]
[Please login or register to view this link]
[Please login or register to view this link]
[Please login or register to view this link]
[Please login or register to view this link]
[Please login or register to view this link]
[Please login or register to view this link]
[Please login or register to view this link]
[Please login or register to view this link]
[Please login or register to view this link]
[Please login or register to view this link]
[Please login or register to view this link]
[Please login or register to view this link]
[Please login or register to view this link]
[Please login or register to view this link]
[Please login or register to view this link]
parts list and build instructions
Designator Description QTY Code Check
R1, R4, R5, & R15 4.7Ω 2W Carbon Film Resistor 4 Yellow-Violet-Gold
R2, R10, R11
R12, & R13 100Ω 2W Carbon Film Resistor 5 Brown- Black- Brown
R3, R6, R7
R8, & R9 10Ω 1/2W Carbon Film Resistor 5 Brown-Black-Black
R14 100Ω 5W Metal Film Resistor 1 Brown- Black- Brown
VR1 100Ω 2W Potentiometer 1 Labeled
C1 100~180 pf Silver Dipped Mica Capacitor 1 100~180 / 500V
C2, C3, C4, C9, &
C23 1000 pf Silver Dipped Mica Capacitor 5 1000 or 102 / 500V
C5, C6, C7, C8 .1 uf Ceramic Disc Capacitor 4 104 or .1
C10, C11, C12
C13, & C14 120 pf Silver Dipped Mica Capacitor 5 120 or 121 / 500V
C19, C20, C21, C22
C25, C26, C27, C28 .01 uf Ceramic Disc Capacitor 8 103 or .01
C15, & C16 330pf Silver Dipped Mica Capacitor 2 330 or 331 /500V
C17, & C18 820pf Metal Clad Capacitor 2 820
C24 150 pf Metal Clad Capacitor 1 150
C29 22 uf Electrolytic Capacitor 1 22 uf / 25V
C30 10 pf Ceramic Disc Capacitor 1 10
VC1 Mica Compression Trim Capacitor 1 465
D1 3A / 1000V PIV Silicon Rectifier 1 1N5408
D2 1A / 1000V PIV Silicon Rectifier 1 1N4007
D3 Glass Signal Diode 1 1N4148
D4 LED Indicator assy. 1 Blue LED / Resistor Pkg.
TR1 Driver Section Power Transistor 1 SD1446 / 2SC2879 (See Note)
*Above transistor depends on which model is being constructed – SD1446=650V+ / 2SC2879=650V+ HDV
TR2, TR3
TR4, & TR5 200 Watt RF Power Transistor 4 2SC2879
TR6 NPN Switching Transistor / TO-92 1 PN2222A
CHK5, 8, 9, 10
11, 12, & 13 ½” x ½” Ferrite Core 7
CHK2, 3, 4, 6, & 7 ¼” x ½” Ferrite Core 5
Designator Description QTY Code Check
T1, T3, & T4 ½” x ½” Ferrite Transformer Core 3
T2 ½” x 1” Ferrite Transformer Core 1
T5, T6 ½” x 2” Ferrite Transformer Core 2
SW1 SPST Switch 1
RLY1 DPDT Relay 12V Coil /10A Contacts 1
FAN1 4.7” Fan Assy. 1
FG1 4.7” Fan Guard 1
Conn1, Conn2 Panel Mount SO239 UHF Connector 2
Conn3 ¼” Stereo Phone Jack 1
Cabinet Aluminum Enclosure Assy. 1
HS1 Aluminum Heat Sink 1
CB1 Pre-Drilled Copper Clad Circuit Board 1
CB2 Copper Clad Circuit Board 5-1/8” x 3/4” 1
PS1, & 2 2 Position Pre-Cut Transistor / Pill Strips 2
PS3, & 4 4 Position Pre-Cut Transistor / Pill Strips 2
SCK1 LED Mounting Clip (with D4) 1
KB1 Control Knob 1
WIRE-1 28” Length of #20 Silver/Teflon Wire 1
WIRE-2 108” Length of #16 Silver/Teflon Wire 1
WIRE-3 3” Length of #14 Silver/Teflon Wire 1
WIRE-4 25” Length of #20 Hook-up Wire (Color 1) 1
WIRE-5 18” Length of #20 Hook-up Wire (Color 2) 1
WIRE-6 12” Length of #10 Red Power Cable 1
WIRE-7 12” Length of #10 Black Power Cable 1
COAX 12” Length RG316 Coax 1
HDW1 Hardware Kit (See Below)
SHCS #4 40 x ¼” Socket screw 14
SHCS #6 32 x ¼” Socket screw 12
Pan Head Sheet Metal Screw 6
Pan Head Machine Screw #6 32 x ½” 8
#6 Lock Washer 6
#6 32 TPI Machine Nut 4
#6 Solder Lug 3
Pan Head Machine Screw #8 32 x ¾” 4
#8 Lock Washer 3
#8 32 TPI Machine Nut 4
Rubber Feet 4
Rubber Grommet 1
Scrap circuit board material 1
Heat sink lubricant 1
Label Sheet 1
4” Cable Tie 4
Tools Needed: Standard electronic hand tools consisting of but not limited to:
Diagonal wire cutters (4-1/2” flush-cut are the best)
Needle nose pliers (4-1/2” with 1/8” dia. tips for shaping component leads, not those super long ones.)
Good pair of tweezers (Serrated jaws are best)
De-soldering tools if needed (Solder Wick, Manual solder sucker, Pace or equiv. powered de-solder station)
Everybody has their favorite hand tools that they use to perform a particular task, so the following pages will only list
tools as a heads-up of some special items that are needed. The use of common sense is your best tool.
Assembly Instructions
Step 1
Parts Needed: Heat Sink (HS1)
Circuit Board (CB1)
1ea. 200 Watt RF Power Transistors (TR2)
4ea. SHCS #4-40 Socket Machine Screw
Tools Needed: Ultra Fine Sharpie Marker
Power Drill (Battery powered is best)
1/8” drill bit
3/32” dill bit (#40 size works better)
Center Punch
4-40 Tap & Handle (Needed if 3/32” drill bit used)
Procedure:
1, Enlarge the six holes in the main circuit board as shown in photo frame #1. Position circuit board on top of heat
sink as shown in photo frame #2 with the front edge of the board flush with the front edge of the heat sink.
Center the circuit board on heat sink as to have about 3/8” over-hang on each side. Mark heat sink though the four
holes of board as indicated in the photo.
2, Remove board and enlarge the four holes used to mark the heat sink by using the 1/8” drill bit as indicated in photo
frame #2.
3, Use the center punch to mark drill points on heat sink. Bore the four drill points to a depth of about 3/8 of an inch
with the 3/32” / #40 drill bit. If a 3/32” drill bit is used, then the four holes should be threaded with the 4-40 tap. If a
#40 bit is used, the #4-40 x ¼” screws will self tap.
4, Return board to heat sink and mount with the four #4-40 socket machine screws. Carefully place the power the
transistor in the #2 front cut-out and mark the heat sink at the two transistor mount drill points. Carefully remove the
transistor and do the same with the four rear remaining cut-outs. (The #1 front cut-out is not used for this amp
configuration) Return the transistor to its container. Remove circuit board from heat sink and bore the 10 holes
using the same techniques used in procedure 3 with one exception, after boring the ten holes, dress the surface of the
heat sink so that the bored holes are clean and flush. It is of the utmost importance that when the transistors are
mounted, they make complete and full contact with the heat sink. A good counter sink bit turned by hand can assist in
this task. When finished, slide a straight edge across heat sink to check for inconsistencies.
5, Remount the circuit board on heat sink. At this point, the assembly should look as that in photo frame #3
Step 2
Parts Needed: Circuit board / heat sink assy.
6 ea. Pan Head sheet metal screws
1 ea. DPDT Relay (RLY1)
1 ea.5-1/8” x 3/4” copper clad circuit board (CB2)
Pre-cut transistor / pill strips (PS1, 2, 3, & 4)
Bottom half of aluminum enclosure (Cabinet)
2ea. Panel Mount SO239 UHF connector (Conn1 & Conn2)
4ea. Pan Head machine screw #6-32 x ½”
2ea. #6 lock washer
4ea. 32 TPI machine nut
2ea. #6 solder lug
Tools Needed: Ultra Fine Sharpie Marker
5 Minute Epoxy
#2 Phillips screw driver
Pliers or wrench for #6 machine nuts
Procedure:
1, Mount both SO239 UHF connectors from the inside of the enclosure making sure that the cut-out on the center
conductor of the connector is facing up. Use the lock washers on the upper mounting holes and the solder lugs on the
lower. Tip: Set the nuts on the lower screws so that one of the flats of the nut is facing down as to allow the bending
of the solder lug. This will provide clearance that may be needed later. See photo frame #4 for reference.
2, Bend solder lugs up as shown in photo frame #4. Lower circuit board / heat sink assy. into the enclosure and slide
under the two bent up solder lugs all the way back until it is against the back of the enclosure. At this point the six
mounting holes on the right and left sides of the circuit board should line up with the six pre-drilled holes in the
enclosure. Mount the circuit board to enclosure using at least four of the six pan head sheet metal screws.
See photo frame #5 for reference.
3, Position DPDT relay with the terminals forward, and in such a way that the two terminals of the relay coil are on
the bottom and the relay itself is centered between the two UHF connectors and against the rear panel of the
enclosure. Mark the two front corners of the relay on the main circuit board as shown in photo frame #6. Now
position the 5-1/8” x 3/4” copper clad circuit board (foil side up) just in front of the rear main circuit board mounting
screws; and centered on the main circuit board. Mark the two front corners of the 5-1/8” x 3/4” copper clad circuit
board on the main circuit board as shown in photo frame #6. Remove the 5-1/8” x 3/4” board and relay, and set aside.
Remove the mounting screws, and the main circuit board / heat sink assy. from the enclosure.
4, Reposition on the main circuit board / heat sink assy. the 5-1/8” x 3/4” circuit board and relay. (Remember, the two
coil terminals of the relay are at the bottom) Now position the four transistor / pill strips (foil side up) as shown in
photo frame #7.
It is important to read the following in its entirety, as the next process must be performed in one fluid action.
Once you get a good feel where everything needs to be located, mix some 5 minute epoxy where the final amount of
the two mixed components is about the diameter of a quarter dollar and 3/16” high. The previous statement for the
quantity is just for reference, but should be enough to perform the next process. Once the epoxy is good and mixed,
remove the previously positioned components one a time starting with the first pill strip. Apply a light coating of
epoxy to the bottom, reposition right back where it came from. Do the same with the rest of the pill strips. Now
mount the 5-1/8” x 3/4” circuit board at its assigned location. Take the rest of the mixed epoxy and apply to the relay
and place at its marked position. Now go back and reposition any of the components that may have shifted.
As the epoxy sets, remove any extra that may have oozed over the edge at the rear of the relay.
Take a break and have a cup of coffee. Page5
Step 3
Parts Needed: Circuit board / heat sink assy.
RF Power Transistors (TR1, TR2, TR3, TR4, & TR5)
Ferrite Transformer Cores (T1, T2, T3, T4, T5, & T6)
10ea. #4-40 x ¼” Socket machine screws
Tools Needed: 3/32” T-handle Allen wrench (Regular Allen wrench may be used)
Soldering Iron (A good 40~50 watt iron with a 1/16” chisel tip is best)
60/40 resin core solder or equiv. (We use Kester 63/37 @ .031”)
Scrap circuit board material (Included in hardware kit)
Heat sink lubricant (Included in hardware kit)
X-acto knife or Olfa knife
Small 1/8” blade straight slot screw driver (Jewelers type is best)
Procedure:
1, Make sure that all five transistor mounting wells are clear of epoxy ooze (Trim with X-acto knife if needed) and
clean heat sink in the transistor wells with a Q-tip to remove any debris. Trim the corner of the plastic bag containing
the heat sink lubricant. Squeeze equal amounts of lubricant into the center of each transistor wells until all of the
lubricant is used. Align the transistor marked SD1446 / 2SC2879 (TR1) over the front well shown in photo frame #8.
Notice that the collector leg of the transistor has a bevel cut in it, and should be pointing to the right. Firmly push
straight down on top of the transistor until it is fully and completely seated. Be very careful not to bend the mounting
tabs of the transistor as they are made of soft metal. Seat the other four transistors marked 2SC2879 (TR2, TR3, TR4,
& TR5) in the rear four wells with their collector legs pointing to the rear. When finished, the assy. should look just
like photo frame #8.
2, This is another point at which we need to be very careful, as we don’t want to twist off the head of any of the #4-40
socket machine screws. With all the transistors fully seated, thread the machine screws through the mounting tabs of
each of the transistors and into the heat sink. Just make them good and snug, not super tight. Believe me; you don’t
want to have to deal with drilling out a steel #4 screw mounted in aluminum. This is supposed to be fun!
If you used a #40 drill bit when boring the transistor mounting holes, the #4-40 screws will self thread. However if
there is undo resistance, back off a couple turns and them continue the self threading process. Once all the transistors
are mounted, bend the legs as instructed in photo frame #9.
3, Gentlemen, heat up your soldering irons! We will presume you have good soldering skills, so we will not get into a
soldering lesson. However, if there are any questions, please give us a call or Email. Solder the emitter legs of each
transistor to the main circuit board assy. as shown in photo frame #10. Take the 1/2” long ferrite transformer core
(T1) and look at each end, you will notice that on one of the ends, the two brass tubes that comprise the primary
winding is not connected. The non connected side from now on will be referred to as the “front” of this and all
transformers. On the front of the transformer you will also notice that the two solder pads may narrow on one side,
this will be considered the bottom edge and also the side that will be soldered to the pill strips. See photo frame #11.
(On transformers that do not narrow, either edge can be soldered to the pill strips.)
4, Take one of the 1/2” long ferrite transformer cores which will become (T1) and set the front end of the transformer
with the bottom edge down on the pill strip at the base leg of (TR1). Place the scrap piece of circuit board material
under the rear of the transformer to keep it level. Adjust the transformer so that the separation cut in the pill strip is in
the center between the two solder pads of the transformer and the bottom front edge just touches the base leg of the
transistor (TR1). Carefully solder each of the transformer solder pads to the pill strip pads on which they sit by
starting on one side and then moving to the next, while doing so let the base leg of power transistor become soldered
to the pill strip pads as well. Use enough solder as to create a good filet that will help support the transformer. See
photo frame #12. Remove the scrap circuit board material and set aside.
5, Rotate the assy. 180º on the work surface. Take the 1” long ferrite transformer core (T2) and set the front end of
the transformer with the bottom edge down on the pill strip at the collector leg of (TR1). Place the scrap piece of
circuit board material under the rear of the transformer to keep it level. Adjust the transformer so that the separation
cut in the pill strip is in the center between the two solder pads of the transformer and the bottom front edge just
touches the collector leg of the transistor (TR1). Carefully solder each of the transformer solder pads to the pill strip
pads on which they sit by starting on one side and then moving to the next, while doing so, let the collector leg of the
power transistor become soldered to the pill strip pad as well. Use enough solder as to create a good filet that will
help support the transformer. See photo frame #13. Remove the scrap circuit board and set aside.
6, Rotate the assy. to the left 90º on the work surface. Take one of the remaining two 1/2” long ferrite transformer
cores which will become (T4) and set the front end of the transformer with the bottom edge down on the part of the
pill strip that coincides with the base legs of transistors (TR4, & TR5). Place the scrap piece of circuit board material
under the rear of the transformer to keep it level. Adjust the transformer so that the separation cut in the pill strip is in
the center between the two solder pads of the transformer and the bottom front edge just touches the base legs of
transistors (TR4, & TR5). Carefully solder each of the transformer solder pads to the pill strip pads on which they sit
by starting on one side and then moving to the next, while doing so let the base legs of the power transistors become
soldered to the pill strip pad as well. Use enough solder as to create a good filet that will help support the
transformer. See photo frame #14. Remove the scrap circuit board material and set aside.
7, Take the remaining 1/2” long ferrite transformer core which will become (T3) and set the front end of the
transformer with the bottom edge down on the part of the pill strip that coincides with the base legs of transistors
(TR2, & TR3). Place the scrap piece of circuit board material under the rear of the transformer to keep it level.
Adjust the transformer so that the separation cut in the pill strip is in the center between the two solder pads of the
transformer and the bottom front edge just touches the base legs of transistors (TR2, & TR3). Carefully solder each
of the transformer solder pads to the pill strip pads on which they sit by starting on one side and then moving to the
next, while doing so let the base legs of the power transistors become soldered to the pill strip pad as well. Use
enough solder as to create a good filet that will help support the transformer. See photo frame #14. Remove the
scrap circuit board material and set aside.
I know we keep repeating ourselves, but it’s just so we don’t make any mistakes.
8, Rotate the assy. 180º on the work surface. Take one of the two 2” long ferrite transformer cores which will become
(T5) and set the front end of the transformer with the bottom edge down on the part of the pill strip that coincides with
the collector legs of transistors (TR2, & TR3). Place the scrap piece of circuit board material under the rear of the
transformer to keep it level. Adjust the transformer so that the separation cut in the pill strip is in the center between
the two solder pads of the transformer and the bottom front edge just touches the collector legs of transistors (TR2, &
TR3). Carefully solder each of the transformer solder pads to the pill strip pads on which they sit by starting on one
side and then moving to the next, while doing so let the collector legs of the power transistors become soldered to the
pill strip pad as well. Use enough solder as to create a good filet that will help support the transformer. See photo
frame #15. Remove the scrap circuit board material and set aside.
9, Take the remaining 2" long ferrite transformer core which will become (T6) and set the front end of the
transformer with the bottom edge down on the part of the pill strip that coincides with the collector legs of transistors
(TR4, & TR5). Place the scrap piece of circuit board material under the rear of the transformer to keep it level.
Adjust the transformer so that the separation cut in the pill strip is in the center between the two solder pads of the
transformer and the bottom front edge just touches the collector legs of transistors (TR4, & TR5). Carefully solder
each of the transformer solder pads to the pill strip pads on which they sit by starting on one side and then moving to
the next, while doing so let the collector legs of the power transistors become soldered to the pill strip pad as well.
Use enough solder as to create a good filet that will help support the transformer. See photo frame #15.
Remove the scrap circuit board material and discard as it is no longer needed.
Step 4
Parts Needed: Circuit board / heat sink assy.
5 ea. 10Ω 1/2W carbon film resistor (R3, R6, R7, R8, & R9)
5 ea. 120pf @ 500V Silver Dipped Mica Capacitor (C10, C11, C12, C13, & C14)
3 ea. 1000pf @ 500V Silver Dipped Mica Capacitor (C2, C3, & C4)
4 ea. 0.1uf Ceramic Disc Capacitor (C5, C6, C7, & C8)
1 ea. 11” Length of #16 Silver/Teflon wire (WIRE-2)
1 ea. 1A / 1000V PIV Silicon Rectifier (D2) (Small)
Tools Needed: Soldering Iron (A good 40~50 watt iron with a 1/16” chisel tip is best)
60/40 resin core solder or equiv. (We use Kester 63/37 @ .031”)
Procedure:
1, Take the five 10Ω 1/2W resistors, bend and trim as shown in photo frame #16.
Solder these resistors in place as shown in photo frame #17.
2, Take the five 120pf capacitors, bend and trim as shown in photo frame #18.
Solder these capacitors in place as shown in photo frame #19.
3, Take the three 1000pf capacitors, bend and trim as shown in photo frame #20.
Solder these capacitors as shown in photo frame #21.
4, Take the four 0.1uf capacitors, bend and trim as shown in photo frame #22.
Solder these capacitors as shown in photo frame #23.
5, Take the 11” length of #16 wire and make 3 loops through one of the 1/2” x 1/2" ferrite cores (CHK5), strip ends
and bend as shown in photo frame #24. Solder bent end to the middle of the back side of T2, and the straight end to
the 5-1/8” x 3/4” circuit board as shown in photo frame #25.
6, Take the 1A rectifier and attach to the two lower relay coil terminals as shown in photo frame #26, pay attention to
polarity and DO NOT solder yet.
7, Carefully bend-up the two top relay terminals as shown in photo frame #27.
Step 5
Parts Needed: Circuit board / heat sink assy.
1 ea. 13” length of #20 Silver/Teflon wire (WIRE-1)
1 ea. 100pf / 500V Silver Dipped Mica Capacitor (C1)
1 ea. 8” length of #16 Silver/Teflon wire (WIRE-2)
1 ea. 25-1/2” length of #16 Silver/Teflon wire (WIRE-2)
1 ea. 1000pf / 500V Silver Dipped Mica Capacitor (C23)
1 ea. 150pf Metal Clad Capacitor (C24)
1 ea. 45” length of #16 Silver/Teflon wire (WIRE-2)
2 ea. 1/2" x 1/2" Ferrite Core (CHK12, & CHK13)
1 ea. 100Ω 5 Watt Metal Film Resistor (R14)
1 ea. 1” Length of #16 Silver/Teflon wire (WIRE-2)
Tools Needed: Soldering Iron (A good 40~50 watt iron with a 1/16” chisel tip is best)
60/40 resin core solder or equiv. (We use Kester 63/37 @ .031”)
Procedure:
1, Take the 13” length of Silver/Teflon wire and trim 1/4"of insulation from one end only. Insert the non-stripped end
of the wire into the right tube of transformer (T1), bend down the stripped end and solder to the main board as viewed
in photo frame #28. Thread the wire through the left tube from the rear and back through the right tube from the
front. Keep doing this until five (5) winding turns are made, always try to keep the current turn on top of the
previous, however if the windings bundle-up it’s OK, see photo frame #29. Prepare the 100pf capacitor as shown in
photo frame #30. Solder the capacitor to the main circuit board as shown in photo frame #31. Wrap the free
capacitor lead around the stripped wire that exits transformer (T1). Solder and trim capacitor lead, but Do Not trim
the transformer wire as shown in photo frame #32.
2, Rotate circuit board / heat sink assy. 180º. Take the 8” length of #16 Silver/Teflon wire and trim 1/4"of insulation
from one end only. Insert the non-stripped end of the wire into the left tube of transformer (T2), bend down the
stripped end and solder to the main board as viewed in photo frame #33. Wind the transformer in the same manner as
you did with transformer (T1) with the second winding on top of the first, but this time we only need two (2) winding
turns as shown in photo frame #34.
3, Rotate circuit board / heat sink assy. to the left 90º. Take the 25-1/2” length of #16 Silver/Teflon wire, straighten
and fold exactly in half. Mark the center, and trim away 1/4" of insulation from both sides of the center line, for a
total of 1/2" insulation removed. Bend the wire to form the shape shown in photo frame #35. Take one of the
1/2" x 1/2" ferrite cores (CHK12), which will become the power splitter (SLT1) and place over one of the legs of the
wire, slide the core up the wire to within 3/8” of the little loop you just created. Bring the other leg of the wire around
and insert it in the other side of the core, pull tight and re-adjust until this assy. is like that shown in photo frame #36.
Take one of the wires and bring the end around and insert it in the opposite side of the core, pull through to make a
tight winding on the core, do this one more time for a total of two tight windings. Take the other wire and do the
same as the first, although in the opposite direction. To assist in this task, see photo frames #37, #38, & #39.
4, Take one of the wires of the power splitter you just made and run it through the inner most tube of (T3), now take
the other wire of the splitter and run it through the inner most tube of (T4) as shown in photo frame #40.
Position the splitter itself centered right up between the two transformers. Take the wire that is exiting the rear of
(T3) and pull it forward through the left tube as shown in photo frame #41. Now feed the wire back through the right
tube under the first winding as shown in photo frame #42. (As each of these turns is made, keep them as tight as
possible) Feed the wire back through the left tube again under the previous winding as shown in photo frame #43.
Do this one more time; so that there is a total of three windings on (T3), making sure that each new winding is under
the previous. When done, your windings should look like those in photo frame #44. Now do the same to (T4) with
the other wire. Remember to keep each new winding under the previous, and to have three turns of wire just like
(T3). When you are finished, your work should look like photo frame #45. Trim both wires so that there is 3/4 of an
inch protruding from each of the transformers. Remove 1/4" of insulation from the end of each wire, and solder to the
main circuit board as shown in photo frame #46.
5, Now we are going to build the same type of assy. as the power splitter, albeit with a slight modification. But first,
we need to prepare the relay. Take the 1000pf / 500V silver dipped mica capacitor (C23), bend and trim as shown in
photo frame #47. Take this capacitor (C23) and the 150pf metal clad capacitor (C24) and assemble as shown in photo
frame #48. Solder and trim as shown in photo frame #49. Solder this capacitor assy. to the main circuit board as
shown in photo frame #50.
6, OK, here we go. Take the 45” length of #16 Silver/Teflon wire, straighten and fold exactly in half. Mark the
center, and trim away 1/4" of insulation from both sides of the center line, for a total of 1/2" insulation removed.
Bend the wire to form the shape shown in photo frame #51. Take one of the 1/2" x 1/2" ferrite cores (CHK13), which
will become the power combiner (CMB1) and place over one of the legs of the wire, slide the core up the wire to
within 3/8” of the little loop you just created. Bring the other leg of the wire around and insert it in the other side of
the core, pull tight and re-adjust until this assy. is like that shown in photo frame #52. Take one of the wires and
bring the end around and insert it in the opposite side of the core, pull through to make a tight winding on the core, do
this one more time for a total of two tight windings. Take the other wire and do the same as the first, although in the
opposite direction. To assist in this task, see photo frames #53, #54, & #55.
7, Remove the insulation from the combiner (CMB1) in the two locations as shown in photo frame #56.
Take the 100Ω 5W resistor (R14) and wrap the leads around each of the two wires of (CMB1) where the insulation
was removed, as shown in photo frame #57. Solder and trim as shown in photo frame #58. Take the combiner assy.
and insert one of the wires into the inner most tube of transformer (T5), and take the other wire and insert it into the
inner most tube of transformer (T6). Pull these two wires through the transformers until the loop of the combiner
(CMB1) can rest on the relay terminal as shown in photo frame #59. Take the unattached lead of (C23) and insert it
into and through the loop of the combiner (CMB1) and the hole of the relay terminal, bend the capacitor lead straight
up and trim as shown in photo frame #60. Squeeze this connection with non-serrated pliers and solder as shown in
photo frame #61.
8, With the circuit board / heat sink assy. oriented so that the relay is positioned away from you, feed the wire that
protrudes from the right tube of (T5) and insert it into the left tube and pull tight as shown in photo frame #62.
Now take the wire and feed it back through the right tube, pulling toward you while keeping it under the first winding.
After pulling the wire tight, it should look like that in photo frame #63. Keep threading in and out of the transformer
until there are three windings on (T5), remember that each new winding should be under the previous. Refer to photo
frames #64, #65, & #66. Once the windings are nice and tight, trim the end of the wire so that only 1” remains as
shown in photo frame #67. Trim 1/4" of insulation from the end of the wire, and bend around the transformer as
shown in photo frame #68. Solder wire to the main circuit board as shown in photo frame #69. Now perform the
same procedure on (T6), but of course winding in the opposite direction. When you are finished, it should look like
photo frame #70.
9, Take the 1” length of #16 Silver/Teflon wire and remove 3/4" of insulation. The 1/4" of insulation remaining will
hold the strands of wire together. Place this wire across the two top bent terminals of the relay as shown in photo
frame #71. Solder and trim as shown in photo frame #72.
Step 6
Parts Needed: Circuit board / heat sink assy.
1 ea. #465 Mica Compression Trimmer Capacitor (VC1)
2 ea. 4.7Ω Carbon Film Resistor
3 ea. 4-3/4” length of #20 Silver/Teflon wire (WIRE-1)
3 ea. 1/4" x 1/2" Ferrite Core (CHK4, CHK6, & CHK7)
4 ea. 100Ω 2W Carbon Film Resistor (R10, R11, R12, & R13)
4 ea. 0.01uf Ceramic Disc Capacitor (C19, C20, C21, & C22)
1 ea. 1000pf / 500V Silver Dipped Mica Capacitor (C9)
2 ea. 820pf Metal Clad Capacitors (C17 & C18)
2 ea. 330pf / 500V Silver Dipped Mica Capacitor (C15, & C16)
Tools Needed: Soldering Iron (A good 40~50 watt iron with a 1/16” chisel tip is best)
60/40 resin core solder or equiv. (We use Kester 63/37 @ .031”)
Procedure:
1, Take the trimmer capacitor (VC1) and prepare as shown in photo frame #73. Solder to the main circuit board in
such a way that the upper terminal of the trimmer capacitor is under the loop of the power splitter (SLT1) as shown in
photo frame #74.
2, Prepare the two 4.7Ω resistors as shown in photo frame #75. Feed one lead of the resistor assy. down and through
the loop in (SLT1) and the hole in the upper solder tab of (VC1), wrap around and trim as shown in photo frame #76,
(Notice the orientation of the resistors to chose the correct lead to attach). Solder as shown in photo frame #77.
Strip enough insulation from the wire exiting transformer (T2) so that you can wrap the remaining lead of the resistor
assy. as shown in photo frame #78. Solder and trim as shown in photo frame #79.
3, Take the three 4-3/4” lengths of Silver/Teflon wire and prepare the three ferrite cores (CHK4, CHK6, & CHK7) as
shown in photo frame #80. Take the prepared ferrite core CHK4, and solder the longer lead to transformer (T1), and
the shorter 3/4" long lead to the main circuit board as shown in photo frame #81. Take the prepared ferrite core
CHK6, and solder the longer lead to transformer (T3), and the shorter 3/4" long lead to the main circuit board as
shown in photo frame #82. Take the prepared ferrite core CHK7, and solder the longer lead to transformer (T4), and
the shorter 3/4" long lead to the main circuit board as shown in photo frame #83.
4, Prepare four (4) harmonic suppression feed-back circuits by using the 100Ω resistors, the 0.01uf capacitors and the
instructions in photo frame #84. The next process can be a little tricky to hold with your fingers, so we recommend
using a good pair of tweezers. Solder the capacitor end of the feed-back circuit to the forward pill strip, and then bend
the leads as necessary to reach over to the other pill strip. It’s a good idea to line things up before doing any
soldering. Please see photo frames #85, 86, & 87 for component placement.
4, Take the 1000pf Silver Dipped Mica Capacitor (C9) and trim both leads down to 1/4". (Retain these two clippings
for later use) Solder to the front of transformer T2 as shown in photo frame #88.
5, Solder the body of each of the two (2) metal clad capacitors (C17, & C18) to the right solder pad, flush with the top
edge of transformers (T5, & T6) as shown in photo frame #89.
6, Take the two scrap wire clippings from procedure #4, and bend as shown in photo frame #90.
7, Take one of the bent scrap wire clippings and “Hook” the terminal hole of (C17), and squeeze with non-serrated
pliers as shown in photo frames #91 & #92. Do the same to (C18) with the other bent wire clipping.
8, Solder both capacitor wire attachments as shown in photo frame #93. Bend each wire and trim as shown in photo
frame #94. Solder each wire to the left solder pad of it’s transformer as shown in photo frame #95. When finished,
they should look like photo frame #96.
9, Take both of the 330pf silver dipped mica capacitors (C15, & C16) and trim their leads down to 1/4". Solder one
each to transformers (T3, & T4) as shown in photo frame #97.
Step 7
Parts Needed: Circuit board / heat sink assy.
Switching Transistor (TR6)
Glass Signal Diode (D3)
22uf Electrolytic Capacitor (C29)
10pf Ceramic Disc Capacitor (C30)
2 ea. 1/2" x 1/2" Ferrite Core (CHK8, & CHK9)
2 ea. 6-1/2” Length of #16 Silver/Teflon wire (WIRE-2)
1 ea. 3” Length of #14 Silver/Teflon wire (WIRE-3)
Tools Needed: Soldering Iron (A good 40~50 watt iron with a 1/16” chisel tip is best)
60/40 resin core solder or equiv. (We use Kester 63/37 @ .031”)
Procedure:
1, Take the switching transistor and bend legs as shown in photo frame #98. Attach the 22uf electrolytic capacitor to
the switching transistor as shown in photo frame #99, observe polarity. Attach the glass signal diode to the
transistor/capacitor assy. as shown in photo frame #100, observe polarity. Attach the 10pf ceramic disc capacitor as
shown in photo frame #101. Solder and trim as shown in photo frame #102, Do Not solder the full length of the
twisted leads as they will need to be bent in the following procedures.
2, Take the two legs of the T/R relay drive circuit where (TR6’s) collector and (C29’s) positive lead are twisted
together, and insert through the hole in the relays coil terminal where (D2’s) anode is connected. Insert until the body
of the transistor touches the relay, wrap these leads around terminal and trim as shown in photo frame #103. Solder
as shown in photo frame #104. Take the free lead of the disc capacitor and thread though the hole in the relay
terminal, bend over, and trim as shown in photo frame #105, but Do Not solder. Trim the remaining twisted leads as
also shown in photo frame #105. Solder these leads to the main circuit board as shown in photo frame #106.
3, Take the two (2) ferrite cores, the two (2) 6-1/2” lengths of silver/Teflon wire, and prepare as shown in photo
frame #107. Solder the 3/4" leads of each prepared choke (CHK8, & CHK9) to the rear of each transformer
(T5, & T6) as shown in photo frame #108. Carefully bend down the power chokes and solder their leads to the
5-1/8” x 3/4” copper clad circuit board (CB2) as shown in photo frame #109.
4, Take the 3” length of #14 silver/Teflon wire, and completely remove the insulation. Place the wire on the 5-1/8” x
3/4” copper clad circuit board (CB2) so that it overlaps the leads of the two power chokes just soldered. Over-solder
this wire at the same two points the chokes were soldered exactly as shown in photo frame #110. (This wire is for
current flow reinforcement).
Step 8
Parts Needed: Circuit board / heat sink assy.
1 ea. 3A / 1000V Rectifier (D1)
4 ea. .01uf Ceramic Disc Capacitor (C25, C26, C27, & C28)
1 ea. Aluminum Enclosure assy. (Bottom half)
6 ea. Pan Head Sheet Metal Screws
2 ea. 2-1/4” Length of #16 Silver/Teflon wire (WIRE-2)
1 ea. 1/4" Phone Jack (Conn3)
1 ea. SPST Switch (SW1)
1 ea. LED Mounting Clip (SCK1)
1 ea. LED Assy. (D4)
1 ea. 100Ω 2W Potentiometer (VR1)
1 ea. Rubber Grommet
1 ea. 12” Length Red #10 Power Cable (WIRE-6)
1 ea. 12” Length Black #10 Power Cable (WIRE-7)
2 ea. 1/2" x 1/2" Ferrite Core (CHK10, & CHK11)
2 ea. 4” Cable Tie
Tools Needed: Soldering Iron (A good 40~50 watt iron with a 1/16” chisel tip is best)
60/40 resin core solder or equiv. (We use Kester 63/37 @ .031”)
Procedure:
1, Take the 3A rectifier, bend and solder as shown in photo frame #111A, & 111B.
2, Take the four (4) .01uf ceramic disc capacitors, bend and trim as shown in photo frame #112. Solder two (2) of
these capacitors at each end of the 5-1/8” x 3/4" circuit board as shown in photo frame #113, #114, & #115.
3, It’s starting to come together! Take the Circuit board / heat sink assy. and mount in the bottom half of the
enclosure using all six (6) sheet metal screws as shown in photo frame #116. Bend down both solder lugs as shown in
photo frame #117. Solder both lugs to the main circuit board as shown in photo frame #118.
4, Take one of the 2-1/4” long #16 Silver/Teflon wires, remove 1/4" of insulation from both ends and solder to the
output UHF connector as shown in photo frame #119. Take the free end of this wire and insert it into the relay
terminal as shown in photo frame #120. Squeeze this connection with non-serrated pliers to flatten, and solder as
shown in photo frame #121. Take the other 2-1/4” long #16 Silver/Teflon wire, remove 1/4" of insulation from both
ends and solder to the input UHF connector as shown in photo frame #122. Take the free end of this wire and insert it
into the relay terminal next to the lead from (C30) as shown in photo frame #123. Squeeze this connection with nonserrated
pliers to flatten, and solder as shown in photo frame #124.
5, Install phone jack as shown in photo frame #125, it’s a good idea to leave finger tight, as we might want to rotate
later. Prepare switch as shown in photo frame #126. Install switch as shown in photo frame #127. Install LED
mounting clip as shown in photo frame #128. Prepare LED assy. as shown in photo frame #129. Install LED assy. as
shown in photo frame #130. Prepare and install potentiometer as shown in photo frame #131, #132, & #133.
5, Solder the black lead of the LED assy. to the main circuit board as shown in photo frame #134. Attach red wire of
the LED assy. as shown in photo frame #135. Install the rubber grommet as shown in photo frame #136. Remove
1/2" of insulation from one end of each of the #10 power cables, insert the black cable through the grommet and
solder to the main circuit board, insert the red cable through the grommet, install the two (2) ferrite cores, and solder
to the 5-1/8” x 3/4" circuit board over the current reinforcement wire as shown in photo frame #137
Step 9
Parts Needed: Amplifier Chassis
1 ea. 11” Length #20 Hook-up Wire (WIRE-4)
1 ea. 1/4" x 1/2" Ferrite Core (CHK2)
1 ea. 13-1/4” Length #20 Hook-up Wire (WIRE-4)
1 ea. 12” Length #20 Hook-up Wire (WIRE-5)
1 ea. 5” Length #20 Hook-up Wire (WIRE-5)
1 ea. 100Ω 2W Carbon Film Resistor (R2)
1 ea. 4.7Ω 2W Carbon Film Resistor (R1)
1 ea. 12” Length of RG-316 Coax Cable (COAX)
Tools Needed: Soldering Iron (A good 40~50 watt iron with a 1/16” chisel tip is best)
60/40 resin core solder or equiv. (We use Kester 63/37 @ .031”)
Procedure:
1, Prepare the 11” length of hook-up wire and the 1/4" x 1/2" ferrite core as shown in photo frame 138. Attach but do
not solder the 5” lead to the bottom terminal of the switch (SW1), solder the 3-1/4” lead to the 5-1/8” x 3/4" circuit
board as shown in photo frame #139. Take the 13-1/4” length of hook-up wire and remove 1/4" of insulation from
each end, connect one end to the bottom terminal of the switch (SW1) along with the previously attached and solder
as shown in photo frame #140. (Read note below before soldering!)
NOTE: When soldering wires to the switch, make sure that it is in the “Off” (Lever down) position. Also
solder wires as quickly as possible, as excess heat on solder terminals can damage the switch. Route this 13-1/4”
length of #20 wire as shown in photo frame #141. Before attaching the end of this wire, please study photo frame
#142. Once the terminals of the phone jack are identified, attach wire as shown in photo frame #143.
2, Attach and solder one end of the 12” wire as shown in photo frame #144. Route and attach this wire to the phone
jack terminal that will connect to the “RING” of the phone plug when it is inserted, as shown in photo frames #145, &
#146. Use the two (2) cable ties as shown. Take the 5” length of hook-up wire and remove 1/4" of insulation from
each end, attach and solder one end of this wire to the relay coil terminal that already has the cathode of (D2)
attached, as also shown in photo frame #146. Attach the other end of this wire to the phone jack terminal that will
connect to the “RING” of the phone plug when it is inserted, as shown in photo frame #147.
3, Attach and solder the 100Ω resistor as in photo frame #148. Attach and solder the 4.7Ω resistor as shown in photo
frame #149.
4, Prepare the 12” length of RG-316 coax as shown in photo frame #150, & #151. Attach and solder the end of the
coax that is 5” from the shield grounding point to the center terminal of VR1 as shown in photo frame #152. Attach
and solder the other end of coax as shown in photo frame #153. Shape, and route the coax cable, then solder the
shield grounding point the main circuit board as shown in photo frame #154.
5, Oh, I’m sorry. I forgot to say take a break for coffee. By all means more COFFEE!
Step 10
Parts Needed: Enclosure cover assy.
1 ea. 4.7” 12V Fan Assy. (FAN1)
1 ea. 4.7” Fan Guard (FG1)
1 ea. 1/4" x 1/2" Ferrite Core (CHK3)
1 ea. 4.7Ω 2W Carbon Film Resistor (R15)
1 ea. #6 Solder Lug
4 ea. #8-32 x 3/4" Pan Head Machine Screw
3 ea. #8 Lock Washer
4 ea. #8-32 Machine Nut
Tools Needed: Soldering Iron (A good 40~50 watt iron with a 1/16” chisel tip is best)
60/40 resin core solder or equiv. (We use Kester 63/37 @ .031”)
Procedure:
1, Prepare the 4.7Ω resistor as shown in photo frame #155. Prepare the cooling fan as shown in photo frame #156.
Mount the resistor as shown in photo frames #157, #158, & #159. Cut and trim the red / B+ wire of the fan, and
solder to the loop in the resistor lead as shown in photo frame #160. Take the of the red wire you just cut off and
remove 1/4" of insulation from one of the ends, solder the stripped end to the other leg of the resistor as shown in
photo frame #161. Wrap the wire around the ferrite core (CHK3) three (3) times and route wire as shown in photo
frame #162. Cut and strip the black / B- wire of the fan, and solder to the solder lug as shown in photo frame #163.
Modify this solder lug as shown in photo frame #164 so that it may be threaded on a #8 pan head machine screw.
2, Mount the fan assy. to the enclosure cover exactly as shown in photo frame #165 using the #8 machine screws,
lock washer, and nuts. Photo frame #166 shows top view of cover after the fan assy. has been installed.
3, Set the assembled cover to the side, it’s time to test and calibrate your new amplifier.
Step 11
Parts Needed: Amplifier Assy. (Cover not attached)
Tools Needed: -12~20VDC power supply capable of supplying a constant current of 100 amps or better.
-10/11 meter transceiver with a “Dead Key” of 2~4 watts, and a peak envelope power no greater than
35 watts for the 650V+ model, and 45 watts for the 650V+ HDV model.
-Bird 43 watt meter with “peak reading upgrade” and 1000W/ 25~60 MHz. element or equivalent.
-Coax jumper with PL259 connectors at each end.
-1000W dummy load or antenna system with a good standing wave ratio (SWR).
The following are very useful but not necessary
-Sweep audio generator with an adaptor that mates with microphone plug on transceiver and has a
switch that keys transmitter. (We use a Wavetek model 188)
-100 MHz. oscilloscope (We use a Hitachi model V-1065)
-600 MHz. RF spectrum analyzer (We use a Hameg model HM5006
-Other RF taps and connectors as needed.
Procedure: Basic Calibration & Test
1, Connect amplifier as shown in photo frame #167.
2, Power up transceiver and select a mid-band frequency.
3, Keep amplifier “Off” and peak reading function of power meter “Off”.
4, Adjust the amplifier gain control to full counter clock-wise.
5, With the transceiver keyed, and while saying the word “Audio” into the microphone, observe power meter for
forward deflection.
6, Turn amplifier “On”.
7, Key-up transceiver with no audio and slowly increase amplifier gain control to full clock-wise.
Observe power meter for forward deflection.
8, With the transceiver keyed, and while saying the word “Audio” into the microphone repeatedly at 1 second
intervals, adjust VC1 for minimum deflection. This is to mean that when you key-up the transceiver, and during
the one second pause where there is no audio, the meter will have a specific reading. But when there is audio, the
meter needle will deviate forward; adjust VC1 so that this deviation is at a minimum. This is the Root Mean
Square (RMS) output reading. Never operate where the needle swings backwards, as this is an indication of
transistor saturation.
9, Turn “On” the peak reading function of the meter. Key-up transceiver with audio and observe peak output.
10, See photo frame #168 for performance data.
Step 12
Parts Needed: Enclosure Bottom / Amplifier Assy.
Enclosure Cover / Fan Assy.
12 ea. #6 32 x 1/4” Socket screw
4 #6 Pan Head Machine Screw #6 32 x ½”
4 #6 Lock Washers
4 Rubber Feet
Self Adhesive Label Sheet
Tools Needed: -7/64” T-handle Allen wrench (Regular Allen wrench may be used)
-Soldering Iron (A good 40~50 watt iron with a 1/16” chisel tip is best)
60/40 resin core solder or equiv. (We use Kester 63/37 @ .031”)
Procedure:
1, Take the enclosure cover/fan assy. and position as shown in photo frame #169. Cut back the fan power wire to the
length necessary to allow the wire to be soldered to the lug of the 1/4” phone jack that carries switched supply power.
Remove 1/4” of insulation and solder to the appropriate lug as shown in photo frame #169.
2, Position cover/fan assy. on lower chassis and install twelve (12) #6 32 x 1/4” socket screws as shown in photo
frame #170.
3, Install the four (4) rubber feet using the #6 machine screws and lock washers as shown in photo frame #171.
4, Take label sheet, cut apart, peel, and place on rear panel as shown in photo frame #172.
Congratulations, you are now the proud owner of a high quality
high performance HF linear amplifier that you built yourself!
The more watts you swing, the more people you bring. BREAK!
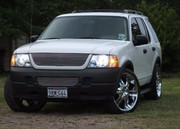
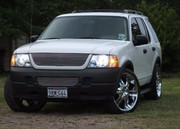
Re: 1X4 Amp Schematics - With Pictures
I merged all 5 topics together.
Special thanks to Westgate for taking the time to post this. I know it takes a lot of time, and it's very appreciated.
Special thanks to Westgate for taking the time to post this. I know it takes a lot of time, and it's very appreciated.